2.1. 배터리 4대 구성 : 양극재, 음극재, 분리막, 전해질
리튬이온 2차전지 기술에서 핵심 요소는 양극재(Cathode), 음극재(Anode), 전해액(Electrolyte), 분리막(Separator) 이다. 각 구성 요소의 구조 및 배터리에서 역할을 이해하는 것은 배터리 기술에서 중요한 내용이다.
[그림] 원형 배터리 단면 구조[우1] (출처 : zeiss.com)

그림은 배터리 단면을 잘라서 보여주는 그림이다. 음극(Anode)은 중앙 구리 Foil에 상하로 음극재가 코팅되어 있는 형태이다. 아래 양극(Cathode)은 중앙에 알루미늄 호일이 있고 상하부가 양극재로 코팅이 되어 있다. Cathode(양극)와 Anode(음극) 사이에는 분리막이 위치하고 보이지는 않지만 전해액이 전체 배터리 내부 전체에 스며들어 있다.
2.2. 양극재 : LCO → NCM
리튬이온 배터리 양극재는 LCO 부터 시작해서 NCM으로 발전해 왔다. 발전 방향은 가격을 낮추고 용량을 늘리기 위한 목적이 가장 크다. LCO 145 mAh/g, NCM 최대 175 mAh/g 까지 용량을 늘릴 수 있다. 하지만 안전성 품질은 LCO가 좋고 NCM은 안정화를 위한 추가의 공정을 추가해야 하는 제조 난이도가 있다.
[그림] 리튬이온 양극재 종류 및 특징
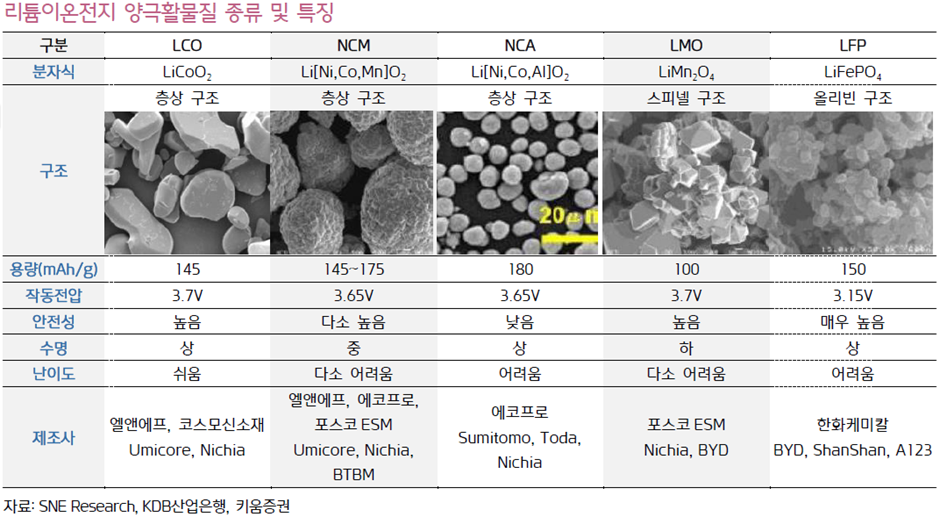
LCO와 NCM의 차이는 입자 형상을 보면 쉽게 이해할 수 있다. LCO는 표면이 매끄럽고 입자가 단순한 구조로 되어 있고, NCM은 작은 입자들이 뭉쳐 큰 입자로 이루어진 구조다.
[그림] LCO, NCM SEM 사진[우1] (Surface morphology)
NCM 입자의 복잡한 구조를 만들기 위해서는 LCO 대비 공정이 추가되어야 가능한 형상으로 기술적인 난이도가 있다.

우측 NCM 제조 프로세스를 보면 LCO 대비 상당히 복잡하다는 것을 알 수 있다. 당연히 제조 단가도 높을 것이다. 중국에서 많이 사용되는 LFP도 LCO와 비슷한 공정 단계를 가지고 있어 제조 단가는 NCM 대비 낮다. NCM 제조 프로세스의 초기 단계가 복잡한 이유는 전구체(Precursor) 제조 단계가 있기 때문이다.
출처 : 코스모신소재 홈페이지
그림은 전구체 제조 프로세스다. LCO(LiCoO2) 전구체는 Co3O4, Co(OH)2, CoOOH이 있으며, NCM, Li(NixCoyMnz)O2 전구체로서는 주로 NixCoyMnz(OH)2가 주로 사용된다. 제조 방법은 주로 공침법으로 제조가 되며, 화학 반응기를 이용하여 금속 혼합용액, 가성소다, 암모니아 등을 공침 반응시켜 제조한다. 반응 조건(조성, 반응온도, pH, 반응 시간, 교반속도, 교반기 종류 등)에 따라 다양한 제품 제조할 수 있다.
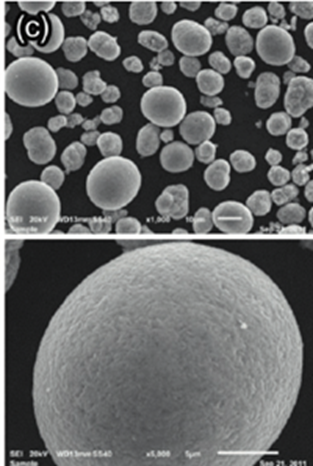
전구체 입자 형태는 완성된 양극재와 아주 비슷하다. 양극재는 전구체 입자에 추가 코팅으로 하므로 입자 표면이 더 거칠어져 보인다. LCO, LFP는 전구체가 없고 전구체 이후 단계는 NCM과 비슷한 공정이다. NCM 제조 공정 흐름은 다음과 같다.
NiSO4 + MnSO4 + COSO4 → 전구체
전구체 + LiOH +첨가재(도핑물질) → 혼합 → 소성1 → 분쇄 → 세정 → 코팅 → 소성2 →포장
NCM 원재료 3가지를 섞어서 전구체를 만들고 리튬과 기능성 첨가재를 넣어 혼합하여 도자기를 굽듯이 시간을 두고 열을 가하는 소성을 하게 되면 1차적인 입자가 형성된다. 입자 크기를 일정하게 만들기 위해서 분쇄를 하고 불순물 등을 제거하기 위해 세정을 하고 다시 기능성 첨가재를 넣기 위해 코팅을 추가할 수도 있다. 코팅 이후 2차 소성을 통해서 최종적으로 원하는 양극재를 제조하는 것이다.
[그림] 양극재 소성 설비

(출처 : 포스코케미칼 구미 공장의 양극재 소성 공정)

소성로에 투입되는 유사 그림
양극재 제조 핵심 공정은 소성 공정이다. 투입되는 원재료 혼합 공정은 무게를 측정하고 넣어서 혼합하는 간단한 방법이지만 소성은 50 미터 정도되는 길이가 긴 설비 구간에서 열을 소성 구간별로 일정하게 관리하고 소성할 때 발생하는 가스 배출 기술 등 양극재 품질을 좌우하는 제조 공정이다. 이런 소성 공정 품질을 일정하게 유지하는 제조기술이 양극재 기업의 핵심 노하우다.
[그림] 전구체 – NCM – 코팅 NCM[우1] 제조 사례
그림은 NCM811 전구체에 LiOH를 Calcination(하소)하고 Carbon Black(탄소)를 Heat-treatment(열처리)로 양극재 입자 표면에 Carbon layer를 코팅하여 기능을 높이는 공정 흐름을 보여준다. 일반적은 양극재에 열을 가하는 공정을 기술적으로 구분하면 소결(Sintering), 하소(Calcination), 소성(Firing), 열처리(Heat-treatment) 4가지로 분류한다. 이 책에서는 소성이라는 용어로 포괄적으로 사용한다.
소성 공정을 마치게 되면 양극재 덩어리를 일정한 크기로 만들기 위해서 분쇄 공정을 거치게 된다.
출처 : JBM PRISPAC SOLUTIONS 홈페이지
그림은 일반적으로 많이 사용되는 Jet Mill 설비 원리이다. 소성이 끝난 덩어리 입자를 Fennel에 넣고 강한 에어가 분사되는 밀폐된 공간에 넣어 양극재가 회전하면서 서로 부딪히면 양극재 입자 크기가 점점 작아지게 된다. 일정한 크기가 되면 입자가 위로 솟아오르게 되고 밖으로 빠져나오는 원리이다. Jet Mill 은 분쇄와 분급이 동시에 일어나는 마이크로 단위 입자를 제조하는 효과적인 설비이다.
[그림] 양극재 입자 분포 (PSD, Particle-Size Distribution)
일반적으로 양극재, 음극재 입자 사이즈는 중심값(D50) 5 ~ 15 ㎛ 으로 설정한다. 양극재는 수많은 입자로 구성되어 있어 입자별로 측정할 수 없다. 그래서 입자 분석 장비인 laser diffraction particle size analyzer 를 이용해서 입자 크기를 측정한다. 그림(a) 입자 크기는 12㎛ 크기이다. (b) 그림에 이런 입자들이 무수히 많이 있고 양극재 입자 크기는 (c) 와 같이 입자 분포로 표현된다. 이런 입자 분포 그래프는 분석 장비를 통해 자동으로 출력되고 각 분포 구간별 판단 기준이 정해져 있다. (c) 그림과 같이 정규분포 형태가 일반적이나 쌍봉 형태의 양극재도 최근 많이 적용되고 있다.
이런 Jet Mill과 PSD 측정 과정은 음극재 공정도 동일하므로 음극재 부분에서는 중복 설명하지 않는다.
[그림] 하이니켈 양극재 제조 프로세스
그림은 하이니켈 NCM, NCA 양극재 생산기업의 제조 프로세스다. 하이니켈계 양극재는 후처리 공정인 코팅과 열처리가 추가됨을 알 수 있다.
출처 : Arthur Martens et al 2020 J. Electrochem. Soc. 167 070510
양극재 제조 후처리 공정의 예로 알루미늄 코팅 사례를 표현한 그림이다. 코팅 소재는 세라믹, 실리콘, 지르코륨 등 많은 소재가 연구되고 있고 코팅 방식은 대부분 그림과 비슷한 방식으로 입자에 적용된다. 결국 특수 소재 코팅은 (c) 와 같이 입자 표면에 일정한 두께로 고루 코팅할 수 있는 제조기술이 필요하다. 하이니켈로 갈 수록 이 후처리 제조기술 중요성이 높아지고 있다.
'리튬이온 배터리 산업편' 카테고리의 다른 글
이차전지 K배터리 산업 : 단결정 양극재 기술 (0) | 2024.12.01 |
---|---|
이차전지 K배터리 산업 : 하이니켈 양극재 기술 (0) | 2024.12.01 |
이차전지 K배터리 산업 : 배터리 기본 동작, 어떻게 동작하나? (0) | 2024.12.01 |
이차전지 K배터리 산업 : 배터리 차세대 원재료 (0) | 2024.12.01 |
이차전지 K배터리 산업 : 배터리 원소재들 리튬 니켈 코발트 (1) | 2024.12.01 |